零件磁场强度检测
来源:忠科集团
忠科集团提供的零件磁场强度检测,零件磁场强度检测是一种非接触性的磁性能检测技术,主要用于检查和评估金属或合金部件的磁通密度、磁感应强度和磁场强度等磁性能参数,报告具有CMA,CNAS认证资质。
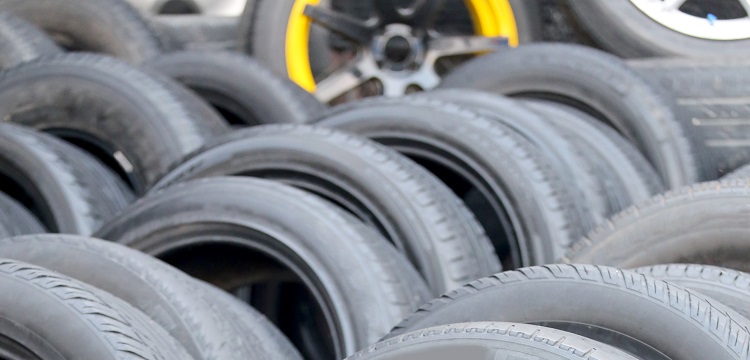
零件磁场强度检测是一种非接触性的磁性能检测技术,主要用于检查和评估金属或合金部件的磁通密度、磁感应强度和磁场强度等磁性能参数。以下是一些常见的零件磁场强度检测方法:
1. 磁化:首先,通过一个磁场源(如交流或直流发电机)产生一个特定频率的电磁场。该磁场与被测材料形成相互作用,使得样品中的自由电子在磁场的作用下受力而运动,形成电流。这个过程通常称为磁化。
2. 激励:激励电路是用于控制磁场强度的设备,通常采用电动机或者电感器来实现。当磁化的工件受到外加磁场激发时,其内部产生的磁场就会增强或减弱,从而测量出相应的磁通密度、磁感应强度或磁场强度。
3. 光学检测:在某些情况下,可以通过光谱仪或X射线衍射仪对磁导率、磁矩和磁通密度等磁性参数进行成像分析。这些仪器可以清晰地显示出材料的磁化状态和变化趋势,从而提供一种直观的判断方式。
4. 电磁超声波检测:这是一种利用电磁超声波在磁场中传播特性,结合声速与磁通密度的关系进行的检测方法。通过发射并接收超声波信号,可检测出工件内部是否有磁性物质的存在,并能够测量出它们的大小和分布情况。
5. 特殊工艺试验:在某些特殊应用领域,例如汽车制造、航空航天、能源工业等领域,可能需要进行专门设计和制造的测试工况。在这种条件下,通过在材料表面涂覆一层特殊的氧化层或者处理介质,可以改变其磁通密度和磁场强度,以便于进行高精度的测试和评估。
总的来说,零件磁场强度检测的方法多样,根据实际需求和材料特性选择合适的方法可以帮助有效地评估和维护金属或合金部件的磁性能,确保其在使用过程中始终保持良好的工作状态。
零件磁场强度检测标准
零件磁场强度的检测通常涉及以下几个方面:
1. 设备和环境条件:确定测量设备、传感器位置以及测试环境的具体参数,如磁场强度范围、温度、湿度、电磁干扰等。这些因素直接影响到磁通量的测量结果。
2. 电流类型和频率:根据被测零件的形状、尺寸和工作状态选择适当的电流类型(例如直流或交流)及频率(如工频或中频)。不同类型的电流具有不同的磁场强度和变化速率,因此选择适合的电流类型和频率是必要的。
3. 测量方法:常见的磁通量检测方法有电感法、电容法、霍尔效应法和涡流法等。其中,电感法主要用于线性结构的磁通量测量;电容法适用于带电金属部件;霍尔效应法适用于矩形或圆形的非线性物体;涡流法适用于铁磁材料(如齿轮、螺母、滑块等)。
4. 磁场源和测量面积:根据磁通量的计算公式(B = I \* A),确定所需磁通量传感器的数量和放置方式。在实际应用中,常常采用多个传感器以提高测量精度和范围。
5. 数据处理和分析:将收集到的测量数据进行统计分析,如平均值、最大值、最小值、标准偏差等,以便评估磁通量的均匀性和一致性。此外,还可以使用相关性分析、误差分析等方法,探讨影响磁通量的因素,为优化设备性能和设计提供依据。
6. 记录和报告:制定详细的测量记录,并在完成测量后编写详细的测试报告,包括测量目的、设备配置、测量过程、测量结果、分析与讨论等内容,便于后续维护和改进。
以上是零件磁场强度检测的基本要求,具体的检测标准会因具体应用场景和仪器设备而有所不同。在实际操作过程中,应遵循相关行业规范和技术指南,确保测量结果的准确性和可靠性。
零件磁场强度检测流程
零件的磁场强度检测通常包括以下几个步骤:
1. 设备准备:首先,需要根据被测零件的特点和预期测量范围选择合适的设备,例如磁化电流表、磁性材料探测器或磁场增强设备等。此外,还需要准备好相应的测试条件,如测量环境、检测频率、检测方式(如线圈法、接触法等)以及电源。
2. 磁场参数设定:在设备启动之前,需要对磁场参数进行设置,如确定磁场强度的最大值、最小值、连续值等,并根据被测零件的具体特性确定测量点的位置和分布方式。同时,也需要考虑环境因素的影响,如磁场强度的变化可能会影响检测结果的准确性。
3. 传感器布设:将传感器安装在与被测零件接触的地方,以确保准确地测量其磁场强度。常用的传感器类型有电磁感应式传感器、热敏电阻式传感器、应变式传感器等,其中电磁感应式传感器由于其相对精度高、耐腐蚀性强,因此在实际应用中常常被用于测量大型或精密零件的磁场强度。
4. 测量过程:在设备运行时,通过特定的方式(如扫描或者接触法)与被测零件直接接触,记录下磁场变化的过程。具体的测量方法可能会因设备的不同而有所不同,但一般来说,会遵循以下步骤:
初始化:设定测量参数后,开始加载初始磁场;
激励:在被测零件接近检测位置的过程中,持续施加激励源,使得传感器接收到一个正弦波信号,从而触发磁化;
振荡时间:根据被测零件的尺寸、形状、材料等因素,确定适当的时间间隔来振荡激励源,保证磁化强度在被测零件达到最大或最小值前均匀持续;
数据采集:在测量过程中,系统会实时记录磁场强度的变化信息,生成检测报告。
5. 数据分析与处理:收集到足够的测量数据后,通过对数据进行处理和分析,可以得到被测零件的磁场强度值。常见的数据分析方法有统计回归、信号处理等,这些方法可以帮助我们识别和量化零件的磁场异常情况,为后续的故障诊断提供依据。需要注意的是,在数据分析过程中,需确保数据的完整性和准确性,避免因数据缺失或噪声过大导致的分析误差。
6. 结果评估:基于处理后的数据,对检测结果进行评估,判断是否存在明显的磁场异常现象,以及这些异常是否与零件的使用环境、机械性能、工艺缺陷等因素有关。对于某些重要部件,可采用进一步的检测手段,如X射线探伤、超声波检测等,以确认问题的性质和严重程度。
7. 批判及处置:如果发现存在明显的磁场异常,应立即通知设计单位或相关方,以便及时采取相应的措施进行修复或更换。对于在正常工作条件下难以检测出的特殊环境或特殊工况下的零部件,可能需要借助专业的技术手段,如磁场预测软件等进行预估和预防性维护。
以上就是零件磁场强度检测的基本流程,具体操作可能因不同设备、应用场景和个人经验而略有差异,但在大多数情况下,上述步骤是不可或缺的,能够有效保障零件的安全性和可靠性。