断裂标称应变
来源:忠科集团
忠科集团提供的断裂标称应变,断裂标称应变是指在断裂前,材料的受力状态或应力-应变关系达到一定值时,当外载荷卸除后,材料内部由于热膨胀、体积收缩或其他因素的作用而产生的一种微小变形,报告具有CMA,CNAS认证资质。
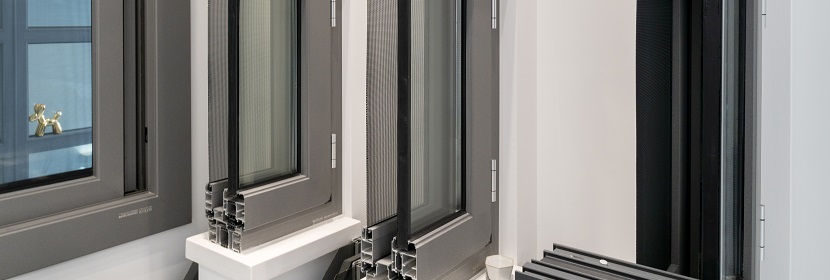
断裂标称应变是指在断裂前,材料的受力状态或应力-应变关系达到一定值时,当外载荷卸除后,材料内部由于热膨胀、体积收缩或其他因素的作用而产生的一种微小变形。这个变形量被称为断裂标称应变。
断裂标称应变的计算通常基于以下公式:
\[
\sigma_{c} = \frac{1}{2} \rho \left( L / c_{a}^2 \right) \cdot V_{a}
\]
其中:
- $\sigma_{c}$:断裂标称应变(通常是负值),单位是帕斯卡·米/千克·毫米。
- $\rho$:材料的密度,常数为0.8克/立方厘米或7950千克/立方米(根据不同的应用和行业标准)。
- $L$:材料的长度,单位是米(m)。
- $c_{a}$:材料的屈服强度,即在给定应力下其允许的最大拉伸应力,单位是帕斯卡(Pa)。
- $V_a$:材料的体积变化率,通常以百分比表示,单位是%。
对于一个特定的材料,断裂标称应变通常与以下几个因素有关:
1. 材料的物理性质:材料的硬度、塑性、弹性模量等都可能影响其断裂标称应变。例如,钢的断裂标称应变通常较低,因为钢具有较高的塑性和弹性模量,使得它在剪切应力作用下容易发生显著的形变。
2. 材料的几何形状:材料的截面形状、边缘角等因素也会影响断裂标称应变。长方形材料往往比圆形或椭圆形材料更容易发生断口,因为这些形状可以减少材料的厚度损失。
3. 外部条件:包括外力的大小、方向以及加载速度等都可能影响断裂标称应变。高应力和大加载速率可能会导致材料在短时间内产生巨大的变形,从而超过其最小可承受应变,引起脆性断裂。
4. 环境温度和湿度:环境温度和湿度对材料的变形有重要影响,特别是对于需要长期保存或者受潮的材料,随着温度的升高和湿度的增加,材料的微观结构会发生变化,可能导致断裂标称应变增大。
因此,要得到一个具体的断裂标称应变值,通常需要使用专门的测试方法,如拉伸试验、弯曲试验、声速测试等,通过测量材料在不同应力水平下的初始应力值、在该应力水平下发生的位移量以及最终拉伸到的应变值来计算断裂标称应变。
断裂标称应变标准
断裂标称应变标准是指用于衡量材料或设备在受外力作用后,其内部结构发生明显变化的特性指标。这个值通常是以百分比形式表示,具体的数值范围和单位可以根据需要进行选择。
以下是一些常见的断裂标称应变标准:
1. 塑性(PSI):这一标称应变标准适用于塑性材料,如混凝土、木材等,其单位通常是帕斯卡(Pa),表示材料承受一定应力时,在受到破坏之前就可能达到的最大变形量。
2. 强度极限(SLN):对于某些特殊结构,例如钢结构、桥梁结构等,可能会采用强度极限作为断裂标称应变标准。例如,对于3/4英寸(约76mm)直径的钢棒,其强度极限可以设定为300MPa,这意味着当其承受超过300 MPa的拉伸应力时,就会发生断裂。
3. 弹性模量(E):弹性模量是衡量材料韧性的重要指标,它反映了材料抵抗形变的能力。一般来说,高强度钢材的弹性模量大于普通钢材,这是因为钢材中的碳原子之间形成的共价键可以更有效地降低形变的可能性。
4. 蠕变极限(TN):蠕变极限指的是材料在应力作用下开始产生不均匀形变的时间点。在某些复杂环境下,如海洋环境、地下环境等,可能需要使用蠕变极限来评估材料在长时间应力作用下的稳定性。
5. 抗拉强度极限(HRM):对于具有较高抗拉强度的钢材,通常会将它的抗拉强度极限作为断裂标称应变标准,这反映了钢材能够承受的最大拉伸载荷。
以上只是一些常用的断裂标称应变标准,不同的应用场合和设计要求可能需要选用不同的标准。在实际工程中,对材料的断裂应变分析往往需要结合材料的具体性质、力学性能以及应用场景等因素来进行综合判断和计算。
断裂标称应变流程
断裂标称应变流程通常涉及到以下几个步骤:
1. 数据收集:首先,需要从多个不同设备或仪器中获取与断裂相关的应变数据。这可能包括但不限于静载荷试验、动载荷试验、弹性模量测试、抗拉强度测试、剪切力测试等。
2. 预处理:对原始数据进行初步的清洗和处理,以去除噪声和异常值。这可能包括剔除重复数据、转换测量单位、标准化应变测量值等。
3. 应力计算:根据已知的材料性质和断裂标准,应用相应的应力分析方法(如泊松比法、拉伸/压缩比法、斜压加载法等)来计算试样的应变。这些方法会考虑物理属性的变化,如线形响应、非线性反应、体积效应等。
4. 压力模拟:基于应变数据的计算结果,建立并模拟试验过程中所施加的压力环境。这可以模拟实际使用条件下的压力分布,例如温度、湿度、压力等级等,以评估试样在不同压力下的应力响应情况。
5. 应力检测:将模拟的压力环境传递到试样上,通过监测试样的应力变化来确定其断裂状态。通常采用动态应变测量技术,如压力位移传感器、应变片等。
6. 评价与结论:根据应力检测的结果,对试样的断裂过程进行定性和定量的评价。如果试样在某个应力级别出现明显的应变变形,可判断其已经达到了断裂的标准,或者对现有设计参数进行了合理的调整和优化。同时,也可以对断裂过程中的其他重要因素,如应力循环次数、塑性转变路径、剪切应力分布等进行深入分析,以提供更全面的参考依据。
7. 报告编写:最后,将评定后的应变信息和相关结果形成一份详细的报告,包括实验目的、方法、结果分析、结论等内容。报告应包含足够的工程背景、实验设计、数据分析、结论等内容,以便于后续的设计决策和施工实施。
需要注意的是,不同的断裂标准和试验条件可能会有不同的要求和取值范围,因此在实际操作中需要根据具体情况进行适当的调整和扩展。此外,任何断裂研究都应在严格遵守相关法规和标准的前提下进行,以确保结果的可靠性、准确性和可信度。