油压-气压测密封性
来源:忠科集团
忠科集团提供的油压-气压测密封性,油压和气压在机械设备、管道系统等工程中常用于检查其密封性能,具体包括以下几个方面: 1.密封性设计:在设计和制造设备时,需要确保各部件之间具有良好的密封效果,报告具有CMA,CNAS认证资质。
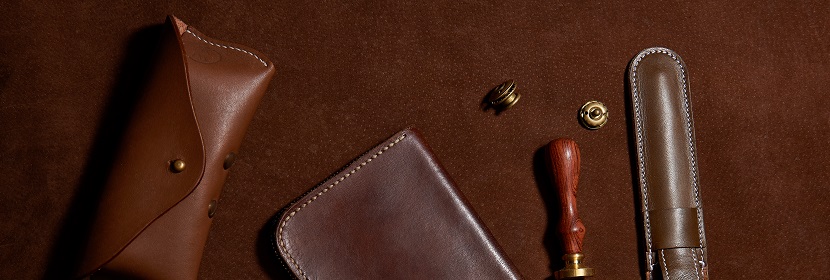
油压和气压在机械设备、管道系统等工程中常用于检查其密封性能,具体包括以下几个方面:
1. 密封性设计:在设计和制造设备时,需要确保各部件之间具有良好的密封效果。油压和气压的测量可以通过泄漏量、压力降或压力恢复时间来评估密封件(如阀、密封圈、垫片等)的工作状态和严密程度。
2. 管道密封性能:在输送液体或气体的过程中,管道内部可能存在多种不同类型的密封材料,例如金属、橡胶、塑料、石棉、填料等多种。油压和气压的测量可以反映这些材料之间的结合强度、压缩系数、剪切变形能力和膨胀率等因素,以判断管道在运行过程中是否存在泄漏现象。
3. 设备运动部件密封性能:例如,液压缸、气动马达、压缩机、涡轮增压器等装置中的活塞杆、活塞环、轴承滚子等关键零部件的密封性能也会直接影响到整个系统的正常工作。油压和气压的测量可通过它们在高压下长时间工作的稳定性、摩擦力和噪音水平等方面进行评估。
4. 气体输送系统的密封性:气体输送系统中的密封元件主要包括管道连接、法兰、阀门、过滤器等。油压和气压的测量可以反映这些元件在实际使用中的密封状况,例如密封面是否光滑、是否泄漏、密封圈材质选择是否正确以及材料力学性能如何等。
5. 安全防护:在化工生产、石油钻井等领域,对精密仪表和电气设备的安全保护至关重要。油压和气压的测量通过检测仪表和线路的泄露情况,能够有效防止设备因漏气引发的事故,保障操作人员的生命安全和财产安全。
6. 能源效率:通过测量油压和气压的变化趋势,可以推断出在某段时间内设备能源消耗的大小,从而对设备的运行效率和节能策略做出调整。
综上所述,油压和气压测密封性是通过多种参数综合评价设备及系统在密封工作过程中的动态特性,从而为设备维护、改进和优化提供科学依据。
油压-气压测密封性标准
在液压系统和气动系统中,油压-气压测试主要用于检查两个独立的密封件(如活塞环、活塞杆或连杆)之间的紧密性和密封性。以下是一些常用的油压-气压测试标准:
1. 密封性试验标准:
- 环向间隙:通过测量活塞环与缸壁之间的径向距离来确定密封性能。该值应小于0.25mm。
- 法兰垫圈厚度和长度:这可以用来评估连杆处的密封性,因为法兰垫圈是连接活塞环与连杆的关键部分。其厚度应该小于或等于活塞环厚度的一半,并且长度应该足够紧贴整个活塞环以保持其功能。
2. 接触面接触质量指标:
- 全部泄漏量:在一定条件下,测试一个单独零件的压力变化对整个系统的压力响应能力,这被称为全泄漏率。如果测得的泄漏量超过规定范围,表明可能存在泄露问题。
- 分离泄漏量:通过测试单位时间内漏出的液体量,分离泄漏率可以提供泄漏情况的具体信息,以及泄漏位置可能存在的敏感点。
3. 活塞环密封性参数:
- 螺纹间磨损:检查螺纹间的深度和宽度是否正常,以评估油液的流动性和活塞环的工作寿命。根据国际标准,螺纹间隙应控制在0.08-0.16mm之间。
- 顶部磨损:监测活塞环上端磨损程度,特别是那些用于支撑活塞头或密封环的部分,以确保其能承受足够的载荷并避免开裂。
- 平滑度:通过测量活塞环表面光滑度来评估密封效果,这有助于防止材料内孔中的颗粒进入活塞腔。
4. 外部压力环境因素:
- 温度:检测不同温度下的工作压力下活塞环的性能,特别是对于高压系统,要考虑高温环境可能导致的活塞环变形或磨损加剧等问题。
- 压力波动:定期测量系统在不同工况下的压力波动,例如定期校准仪表或传感器,以保证密封装置在压力波动期间仍能稳定工作。
- 风速:当空气流动速度较快时,密封剂可能受到侵蚀或不稳定,导致泄漏,因此需要测量设备运行过程中风速的变化,并分析其对密封的影响。
综合上述测试标准,可以进行油压-气压测试来确定液压系统或气动系统中的密封性状态,以便及时发现并解决可能出现的问题,提高系统效率和可靠性。同时,这些测试也可以作为设计、生产和维护过程中的参考依据,帮助优化系统的设计和改进策略。
油压-气压测密封性流程
油压-气压测密封性是一种通过测量液压或气体压力与液位差来检测设备、管道或其他封闭空间内部的密封性的常用方法。以下是一个简单的流程步骤:
1. 收集和准备数据: 准备一个包含多个不同密闭空间(如油箱、气罐、阀门等)和一组预设的标准值作为初始基准点,这些标准值将被用于比较实际泄漏情况。
2. 选择测量工具: 根据具体测试场景选择适当的测量工具,如:高压传感器、压力计、数字信号处理器(DSC)、电磁流量计等。如果需要对气体进行测压,可能还需要考虑使用压缩空气发生器和流量计。
3. 设置系统参数: 安装或调整计量设备,并设定测量时所需的流速、压强和环境条件(如温度、湿度等)。这通常会根据具体的测量目标和设备特性和操作要求来确定。
4. 获取样品分析: 将待测系统的样品输送到实验室进行化验。在不同的试验条件下测量每个样品的压力变化(通常为动态测试),记录其对应的液体体积变化或者温度、压力数据。
5. 数据分析与建模: 使用软件进行数据分析,比如Python中的NumPy或Pandas库,基于已采集的数据建立模型,以预测不同工况下各个元件的实际压力损失或气体泄漏量。模型通常包括但不限于定积分、线性回归、随机森林、支持向量机等算法。
6. 对比基准点与真实泄漏数据: 通过对比理论模型预测值与实际泄漏数据,评估系统的密封性能。在每个参数匹配的条件下,计算并报告系统的实际泄漏率。此值反映了实际压力损失与理论值之间的差距,反映系统在特定工况下的密封性能。
7. 检查验证:在选定的测试阶段内,应反复运行实验,确保实验结果的可靠性。通过多次验证和修正,提高模型的精度和稳定性。
8. 校准仪器和设备: 对所有测定设备进行定期校准,确保测量结果的一致性和准确性。
9. 监控和维护:定期监控和维护系统的测试数据,记录每次试验的数据变化趋势和报警信号,及时发现和处理可能出现的问题。
10. 建议改进措施: 根据测试结果提出针对系统缺陷的改进建议,例如更换密封件、优化工艺流程、提升控制系统设计等。
总之,油压-气压测密封性是通过对液压或气体压力与液位差进行实时监测,检测系统在各种工况下的密封性能,从而帮助判断设备、管道或其他封闭空间是否需要进行维修、更换或改造的关键手段。这个过程需要专业的技术和数据分析技能,以及对现场环境和相关设备的深入了解。