工业问题诊断
来源:忠科集团
忠科集团提供的工业问题诊断,工业问题诊断是指在工业生产过程中,通过对生产设备、工艺流程、产品质量、能源消耗、安全生产等方面进行系统性的监测、分析和评估,识别并确定存在的问题及其产生的原因,报告具有CMA,CNAS认证资质。
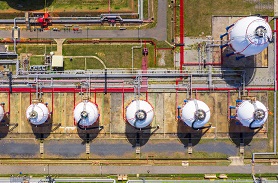
工业问题诊断是指在工业生产过程中,通过对生产设备、工艺流程、产品质量、能源消耗、安全生产等方面进行系统性的监测、分析和评估,识别并确定存在的问题及其产生的原因,进而提出改进措施或解决方案的一种活动。它是确保企业生产效率提升、产品质量稳定、成本控制有效、环境友好以及安全生产的重要手段。这一过程可能涉及设备故障诊断、工艺优化、能效分析、环保监测等多个方面,旨在帮助企业实现持续改进与优化运营的目标。
检测标准
工业问题诊断标准通常会根据不同行业、不同生产环节的特性进行定制,但一般来说,可以从以下几个维度来进行:
1. **生产效率诊断**:包括设备利用率、生产节拍时间、产出率、故障停机时间等指标,看是否存在效率低下、产能浪费等问题。
2. **质量控制诊断**:通过产品合格率、不良品率、返修率、客户投诉率等数据,判断产品质量控制体系是否完善有效。
3. **安全生产诊断**:查看安全事故频率、隐患排查整改情况、安全制度执行情况等,评估安全生产管理是否合规有效。
4. **资源利用诊断**:能源消耗、原材料损耗、废弃物排放等方面的数据分析,评判资源利用效率和环保性能。
5. **设备运维诊断**:设备完好率、故障频次、维修周期、备件库存合理性等,考察设备管理和维护水平。
6. **流程管理诊断**:从工艺流程合理性、操作规范性、信息传递效率等方面评价企业流程管理水平。
7. **人员效能诊断**:员工技能素质、劳动生产率、出勤率、离职率等,衡量人力资源配置与开发的效果。
8. **经济效益诊断**:结合产值、成本、利润等财务指标,对企业的经济效益进行全面审查。
以上各项内容均需要参照国家相关法规、行业标准以及企业内部管理制度进行综合考量和诊断。
检测流程
工业问题诊断流程通常包括以下几个步骤:
1. 问题接收与初步分析:
接收客户请求或报告,了解设备故障、生产异常、质量问题等基本情况。
初步收集相关数据资料,包括设备参数、运行记录、故障现象描述等。
2. 现场勘查:
派遣专业技术人员到现场进行实地考察和详细调查,对设备、工艺、环境等因素进行全面评估。
进行必要的仪器检测、样品采集等工作。
3. 数据收集与分析:
收集详细的运行数据、历史维护记录、产品检验结果等信息。
利用数据分析工具和技术,对收集的数据进行深入挖掘和分析,寻找可能的问题源头。
4. 问题识别与定位:
根据分析结果,识别出可能存在的问题及其可能的原因,包括设计缺陷、操作不当、维护不足、材料老化等。
确定问题的具体位置以及影响范围。
5. 解决方案制定:
针对识别出的问题,研究并制定解决方案,包括改进措施、预防策略、维修方案等,并预估实施效果及成本。
与客户沟通讨论,确保解决方案的可行性和经济性。
6. 实施与验证:
按照制定的方案进行实施,如进行设备维修、工艺调整、人员培训等。
实施后再次收集数据,通过对比分析验证问题是否得到有效解决。
7. 报告编写与提交:
编写详细的诊断报告,包括问题分析、解决方案、实施过程、验证结果等内容。
将报告提交给客户,并进行必要的解释说明和后期跟踪服务。
以上是一个大致的工业问题诊断流程,具体实施时可能会根据行业特性和问题具体情况有所调整。